|
|
|
The Ultra Tec Owners' Newsletter
May 1997
"The Some Times"
|
|
Dear Ultra Tec Cousin,
Well, the Hale-Bopp Comet came - and I took it as an omen to start this
newsletter. Then, the Hale-Bopp Comet went - and I realized I'd better
get working and finish the newsletter before the comet turns around and
heads back again.
To first time readers - welcome to the Ultra Tec faceting family. This
is Joe Rubin writing - in my 25th year with Ultra Tec - the official
company newsletter writer. This is the Ultra Tec Family newsletter -
which Ultra Tec cousins receive with family-letter-like frequency,
hence its name: "The Some Times". If you write back, and we urge you to do
that, it's at your own risk - you might prompt another "Some Times" issue.
Looking back, l see that the last newsletter was early in 1996 - before
the '96 Tucson Show. We haven't been travelling much since then - we went
to Tucson in '96 (but not in '97), and, we went to the Faceting Seminar in
Riverside California last Summer. That's it. No gallivanting around the
Globe, as in other years.
We skipped Tucson this year because of its crazy (I think) '97 format -
spread out over a month, with open dates between the shows. For us, as
manufacturers, it was just not practical. And, for people who might go
to the show, its inconvenience was demonstrated by the poor attendance.
- Now, I am pleased to say, I've heard that the '98 schedule has been
re-thought, and it will return to a compact schedule. I hope those
reports are correct - and that they can put Humpty Dumpty together again.
In any event - we had many interesting first-time meetings in Tucson
in '96-
|
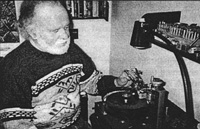
|
We met with Michael Beach, our dealer in the UK (why does "UK" sound
funny? when "US" sounds OK - even "OK" sounds OK). Michael Beach, a
faceter himself, got his FGA degree in 1960, and has been in the
Lapidary equipment business for over 30 years - about the same
amount of time that Ultra Tec has been in business - so he knows
the field, and, he has that many years of good stories! -
including that among his customers and students he counts members
of the Royal Family. We are very happy to have him representing
Ultra Tec - UK cousins can reach M.L. Beach Ltd. at
0181 892 0409.
|
We also met with Ultra Tec representatives Hubert Heldner and
Katerina Kestermont, of Switzerland. Their shop is in Montreaux,
an exceptionally beautiful location on the shores of Lake Geneva.
They are jewellery designers - and they conduct faceting classes.
The class is one day of concentrated work, limited to three students.
The student is provided a very good piece of rough - a tourmaline, or
aquamarine - so that the student takes home a gem of real value, offsetting
the cost of the class. It's an interesting (and successful) approach to
teaching, by interesting and talented teachers.
For those of you who might consider going there, their address is:
Artistes des Bijoux, Grand Rue 83, 1820 Montreux - tel: 021 963 8977/ fax 8978).
|
A SHOW DEMO.
At our booth, Gary Brown, a pro cutter from St. Louis,
asked if he could use an Ultra Tec right there - to cut an Ultra-marine.
It was a welcome idea. Gary had a BIG piece of rough - a 150 carat Aquamarine,
with a "user friendly" shape. To maximize the yield, he cut an original
design - a step cut which yielded 75 carats (the photo gives you
a good idea of its size - l wish the photo could
show you what a handsome stone it is). It's obviously an investment
stone (too big for a pinky ring).
The "demo" lead to good conversation - on two subjects:
|
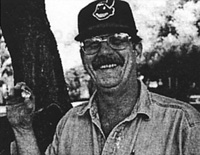
|
WHAT TYPE OF GEM MATERIAL SHOULD A FACETER CUT ?:
The idea was put forward that faceting time should be spent
cutting "good material" (that is, relatively expensive material), and
almost never inexpensive material - like quartz. The idea was endorsed
by the professional cutters present, including Paul Javery, from St.
Croix, Virgin Islands, and Hubert Heldner of Switzerland.
I think anyone must concede their logic - from a financial standpoint,
it's obviously correct: since the value of a cut stone is some multiplier
of the value of the rough, the time spent cutting expensive material
generates more money than the same amount of time spent on relatively
inexpensive material.
There are many faceters, however, for whom the goals and rewards of
faceting are not primarily financial. I fit better in this group myself
(actually, much of my faceting is in evaluation of equipment - and I use
quartz most of the time). Nevertheless, as many of you know, it had long
been my advice to cut the best material that you can afford (is it possible
that I am one of the few people in the world who preach one thing and do
another?). But, the discussions made me think - and inspired me to buy
some nice tourmaline rough - yes, expensive (expensive in my mind). And
I love having those stones, even if I never sell them.
In the process, I also relearned something about buying rough: when you
are ready to actually exchange your hard-earned cash for a rock, you
become an instant expert on selecting good material - detecting flaws,
estimating yield, etc.
POLISHING.
Subject two was POLISHING. This, of course, is a frequent discussion.
This time, the discussers - all pro's - were unanimous. They all endorsed
using the polishing lap that Gary used - a Zinc Lap (I never used one before
- I do now). Zinc Laps have been around - but until recently I'd mostly
heard them recommended for CZ. But those pro's surprised me by recommending
Zinc as the best "general purpose" polishing lap (looking back over my notes,
I see that Paul Javery mentioned that it's not always effective with Quartz,
but that hasn't been my subsequent experience). As we watched Gary Brown
in action with the Zinc lap, he got impressive results in polishing his
large aquamarine.
Before using the Zinc lap, it was prepared by scoring the surface with
radiating scratches - put in with a 260 grit Silicon Carbide paper) - and
of course, well cleaned with water. Then, a film of light oil was applied
to the surface (like a light mineral oil), and a spray diamond applied
(Gary used 14000). Contrary to the polish slowly rule, the lap was run fast,
about 700 RPM (about "7" on the speed control dial). You can "hear" and
"feel" the polish come in. Is this the final end-all of polishing discussions?
- don't bet the farm on it - but Zinc is what I've used most recently, with
happy results.
Incidentally, if you remember several newsletters back, there was the
recommendation to follow any diamond polish (even a 50000 diamond polish)
with a "kiss" on an Aluminium Oxide Ultra Lap - that recommendation still
holds - the bit of "haze" vanishes.
SEMINARS.
Avid readers of this newsletter (can one be avid about a once-a-year
newsletter?) know that I've been recommending attendance to faceting
seminars. Last summer's Southern California Faceting Seminar, in Riverside,
certainly lived up to high standards. Glenn Klein-with the help of his wife
Rhoda and the other members of the SC Faceters Guild - did a super job of
organizing the seminar. I was unable to attend all of the lectures, but I
was particularly impressed by John Sinkankas, who discussed mineral crystal
systems and their effect on cutting any particular stone - does that sound
dry? It wasn't (that's the chapter in the book that I always skipped - but
he gave life to it - and sent me back to my reading). The Seminar deservedly
drew attendees from all over the USA, and I welcomed a chance to chat with
Ultra Tec Dealers Dr. Granville Tabb from Mississippi and Art Grant
from upstate New York.
SEMINAR COMING UP
There's a seminar coming up next month, Midwest Faceters Guild style, in
Hartland, Michigan. It's a 3-day event, August 22 (evening), 23, and 24.
The format consists of classes at several levels ranging from beginner on
up - you do your faceting under an expert instructor's guidance. This year's
staff consists of an impressive line-up of faceters, many of them
award-winners - including Don Dunn, Bill Gardiner and Bill Horton (to
mention people previously highlighted in the "Some Times"). And, several
lectures will be given by Dr. Kurt Nassau - you probably have read some
of his articles in Lapidary Journal.
If you can, go to this Seminar. As someone who went several years ago, l
can tell you: it would be impossible for you not to learn and impossible
not to have fun. Tell 'em Joe sent you.
For details - cost, lodging, program, etc, call: Bill Horton 517 546 2159,
or, Bill Gardiner 517 655 3608, or, Arizona Rice 810 463 5972, or, Kathleen
Myers 517 624 9178.
WHAT'S NEW?
I had once written an article, "Transfer Techniques", which explained how
monoblock (machined out of one piece) designs are inherently more accurate
than designs that have a sliding V-block - and they are. Ultra Tec at that
time was delivering a monoblock design. We stopped sending out that article
when we replaced our monoblock design with a sliding-V-block one,
necessitated (I thought) by the keyed dop system.
There was a short period, however, right when we introduced the keyed-dop
system, during which we continued to supply a monoblock. It was used with
slides that fit the V and in turn held the dops. Some people found it
difficult to manipulate those pieces, however, and we replaced it with, a
sliding-block design. But, the possibility of combining keyed dops with a
monoblock Transfer Fixture continued to rattle around in my mind. It was a
matter of ironing out the "details" - isn't it always? - and we did.
|
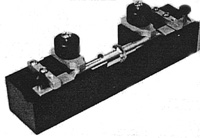
|
A picture is better than 10000 words, and here's the picture:
The new Transfer Fixture is heavier than any preceding Transfer Fixture
- and, with our current manufacturing capabilities, the most
accurate. A nice thing about monoblock designs is that they can be less
expensive. This one is, so we've dropped the Transfer
Block price, as well as the price of the keyed spindle mod of which it is
a part. The enclosed price list will have some details.
|
NEW BOOK
GRAM 1 FACETING DESIGNS by Jeff Graham.
Jeff is a gem cutter, living in Tucson. Jeff's new book is a "labour of
love" - he told me that he's written the sort of book that he wishes he'd
had available earlier in his faceting career. The book includes 56
original never-previously-published designs, divided into sections devoted
to Quartz, Topaz, Beryl, Garnet, Tourmaline, Corundum, and Synthetics.
Making it convenient is its sturdy-cover loose-leaf format (there's a
protective plastic envelope to hold the page you've removed from the book
to work on). This newsletter includes one of his designs, so you can get
an idea of the format. It's interesting to note that if you browse the
designs of particular designers, there's something about them that makes
them recognizable - much like you can recognize the music of particular
composers. That's certainly the case with Jeff Graham's work - and if you
like the taste we've given you in the attached designs, treat yourself
to the book.
MORE ABOUT FACETING CLASSES.
Jeff Graham is associated with Starr Gems in Tucson-and, as long as I've
plugged classes in Switzerland, I should tell you about classes conducted
by Starr Gems - instruction is highly personalized, with a maximum of 3
students per class. Rough and supplies are included - the student
generally completes 2 stones. For more info, call Starr Gems and speak
to Shawn Starr. Their phone number is 602 882 8750.
MISCELLANY:
Yessica Munoz-Cervantes (who is the most likely person to answer the
Ultra Tec phone) is pregnant, and due to give birth in October. She promises
to be back to work (thank goodness) a couple of months later. She's been
with Ultra Tec for 10 years (!), starting out as a part-timer after school
lf you call Ultra Tec after hours ("after hours" is after 5PM - but usually
later than that - on weekdays, and weekends) you will get our answer machine.
The voice you hear belongs to Tim Hazeldine. He recently joined us -
British accent and all - very sophisticated (sounding)
Robert Rubin and Gus Munoz, have taken over many of my
Ultra Tec duties so that I can proceed with my semi-retirement - l actually
took off a few days for a camping trip, with my 4 year old grandson, Michael
(what could possibly be better). Last week, Michael attended the Ventura
County Fair and discovered, and fell in love with - guess - faceting! Someone
was demonstrating faceting, on an Ultra Tec, and Michael realized that's
the machine that Grampa makes. So, excitement abounds - and guess who's
on the hook to facet, for Michael, a simulant of the ring worn by Ringo
Starr in "Help!" (a movie Michael loves) - about a 300 carat ruby?
Donations of rough gratefully accepted (otherwise I have an old ashtray).
Will Grampa do it? Does a bear sleep in the woods?
Robert reminds me to extend a special greeting from him (does he have
designs on this newsletter?)-
ROBERT SEZ:
Ultra Tec has a page on the "Web". You get to it with
www.ultratec-facet.com. Look it over - you can send us a message by email
right off the web page - We'd welcome your comments...designs (perhaps we
can print them and give you the credit - and eternal fame)...jokes? (you
must know a few better than Joe's)....I hate making my first "Some Times"
message one about the computer because I agree with Joe that there's a
disturbing tendency for people to do "virtual faceting" on their computers,
instead of doing real faceting. I think real faceting will come back strong,
however - when I gave my girlfriend a dazzling originally designed Aquamarine
she was unappreciative (well OK, it was a computer printout thereof -
but still..)...Show: We will be participating in a show (close to home
for us) in Pomona, at the L.A. County Fairgrounds, November 14, 15,
and 16th. The show is hosted by the Mineralogical Society of Southern
California, and the show's theme is "Amethyst". So, if you're in the
neighbourhood at that time, come see us at the show....
Until next time - best wishes from all of us at Ultra Tec.
|
 : |
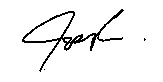
|